Precision Injection Molding: Revolutionizing the Metal Fabrication Industry
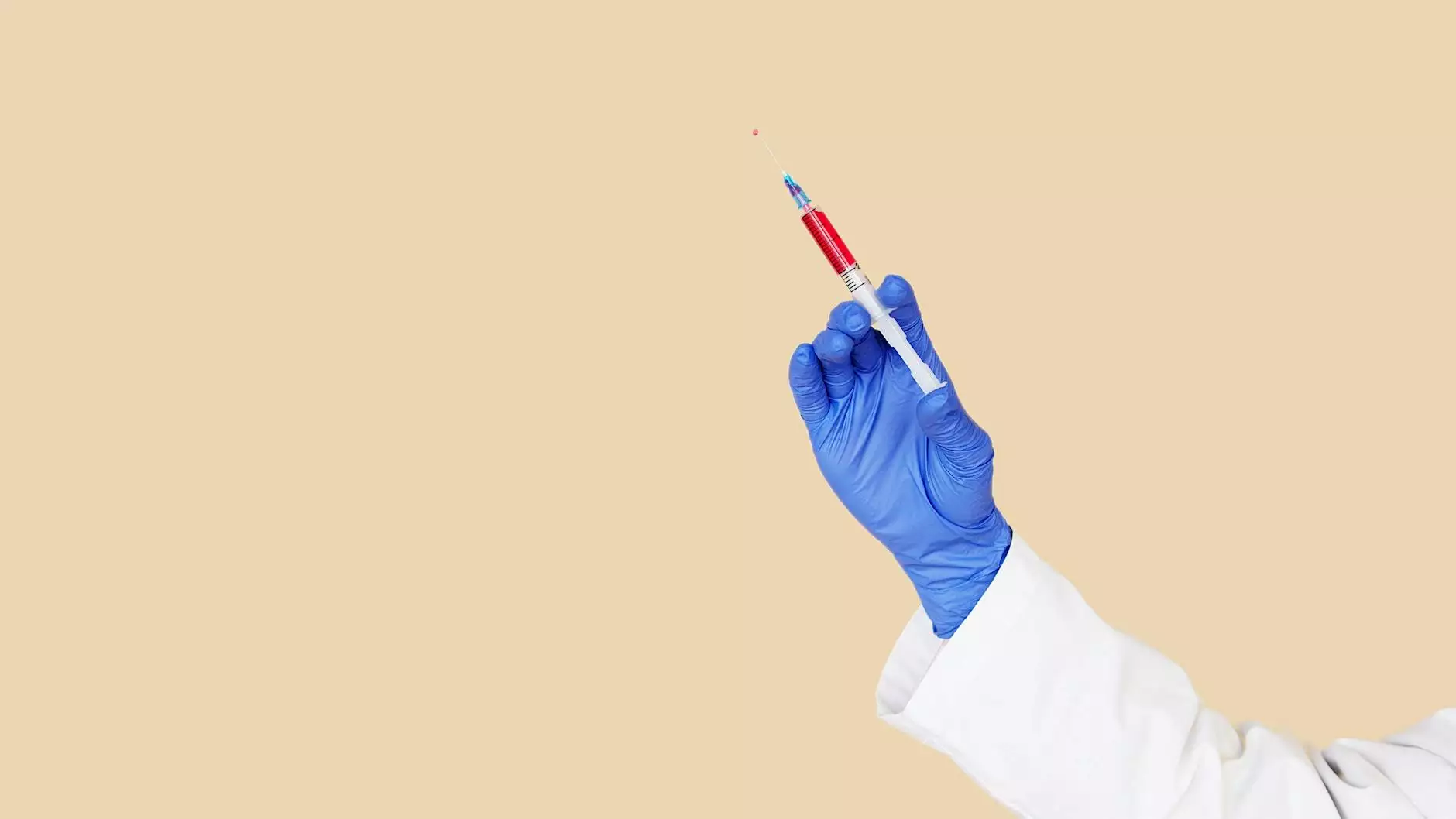
The world of precision injection molding has evolved dramatically over the years, influencing various industries ranging from automotive to electronics. As a core process in the field of metal fabrication, it plays a critical role in creating high-quality, intricate parts with exacting specifications. In this comprehensive article, we will explore the nuances of precision injection molding, its advantages, and its impact on the manufacturing landscape, particularly focusing on its relevance to the category of Metal Fabricators.
Understanding Precision Injection Molding
Precision injection molding is a manufacturing process that utilizes high-pressure to inject molten materials—primarily plastics and metals—into molds. This process is essential for producing parts that require extreme precision, ensuring that each component meets stringent quality standards. The technology behind precision injection molding has advanced significantly, enabling manufacturers to create complex shapes and intricate designs that were previously impossible.
The Process of Precision Injection Molding
The process of precision injection molding can be broken down into several crucial steps:
- Material Selection: The choice of material is paramount. Commonly, thermoplastics and thermosets are used for producing molds, whereas metals like aluminum and steel are typically preferred for durability.
- Mold Design: Engineers design molds using sophisticated CAD software, ensuring that every detail is meticulously mapped out to achieve the desired shape and functionality.
- Injection: The selected material is heated until it reaches a molten state and is then injected into the mold at high pressure.
- Cooling: After injection, the material is allowed to cool and solidify. The cooling time can vary based on the material and the complexity of the part.
- Ejection: Once cooled, the mold is opened, and the finished product is ejected. Precision is crucial during this phase to avoid damaging parts.
- Finishing: Depending on the application, further finishing processes—like trimming, coating, or assembly—may be necessary to ensure the part meets required specifications.
Advantages of Precision Injection Molding
Opting for precision injection molding comes with a multitude of benefits that enhance product quality and manufacturing efficiency. Here are some of the primary advantages:
- High Precision and Repeatability: The primary draw of precision injection molding is its ability to produce parts with tolerances as tight as ±0.01 mm. This level of precision is indispensable in industries like aerospace and medical devices.
- Cost-Effectiveness: Although the initial costs for mold creation can be high, the efficiency of the injection process leads to lower costs per part when producing in large volumes.
- Design Flexibility: Designers can create complex geometries that are lightweight yet robust, which is often unachievable through other manufacturing methods.
- Material Variety: A wide array of materials can be used, allowing companies to choose plastics with specific characteristics (impact resistance, chemical resistance, etc.) optimal for their products.
- Reduced Waste: Precision injection molding produces minimal waste as it allows manufacturers to utilize only the exact amount of material needed for each piece.
Applications of Precision Injection Molding in Metal Fabrication
The applications of precision injection molding are vast and span across multiple sectors within the metal fabrication industry. Here are some key applications:
1. Automotive Industry
Precision injection molding is widely used in the automotive sector to produce components such as:
- Dashboard components
- Interior trim parts
- Engine components
These parts need to meet strict safety and performance standards, and precision manufacturing ensures that they do.
2. Electronics
In the electronics industry, where small form factors and complex designs are common, precision injection molding is employed to create parts such as:
- Connectors
- Housings
- Insulation components
The technology allows for the integration of various features into a single part, simplifying assembly and enhancing reliability.
3. Medical Devices
The medical device industry relies heavily on precision injection molding for components needing high levels of accuracy and cleanliness, such as:
- Syringes
- Implants
- Diagnostic equipment
In medical applications, compliance with health regulations and maintaining sterile conditions is essential, and precision molding helps achieve these standards.
Innovations in Precision Injection Molding
The landscape of precision injection molding continues to evolve through technological advancements. Some notable innovations include:
1. Advances in Material Science
Innovative materials are being developed that enhance the properties of molded parts. Materials with improved strength-to-weight ratios, better thermal resistance, and enhanced electrical properties are paving the way for new applications.
2. Smart Manufacturing Technologies
Integrating IoT (Internet of Things) technology into molding processes has enabled real-time monitoring and adjustments. This leads to improved efficiency, reduced downtime, and enhanced product quality.
3. Eco-Friendly Alternatives
As sustainability becomes increasingly important, manufacturers are exploring biodegradable and recyclable materials for injection molding processes. This reduces environmental impact while meeting market demands for greener products.
The Future of Precision Injection Molding
The future of precision injection molding looks promising, with continuous advancements in technology and materials. As companies seek more efficient manufacturing processes, the demand for high-precision components is expected to grow. Moreover, the integration of automation and artificial intelligence into production lines will further enhance operational efficiencies and reduce lead times.
Choosing the Right Precision Injection Molding Provider
When selecting a provider for your precision injection molding needs, consider the following factors:
- Experience and Expertise: Choose a company with a proven track record in meeting specific industry requirements.
- Technological Capabilities: Ensure they use modern equipment and techniques that can handle the complexity of your designs.
- Quality Assurance: Look for a provider that implements stringent quality control measures at every stage of the production process.
- Sustainability Practices: Consider providers who prioritize eco-friendly practices in their operations.
Conclusion
Precision injection molding is not just a manufacturing process; it is a pivotal force shaping the future of the metal fabrication industry. With its numerous advantages, expansive applications, and ongoing innovations, it establishes itself as a foundation for producing high-quality components across various sectors. As industries continue to evolve, leaning toward precision injection molding will undoubtedly remain a strategic choice for businesses aiming to thrive in a competitive market. For those in the Metal Fabricators category, embracing this technology is essential to staying ahead.
At DeepMould.net, we are dedicated to pioneering advanced precision injection molding solutions tailored to your specific needs. Connect with us to explore how we can enhance your manufacturing capabilities and drive your business forward.