The Essential Guide to Automotive Plastic Parts
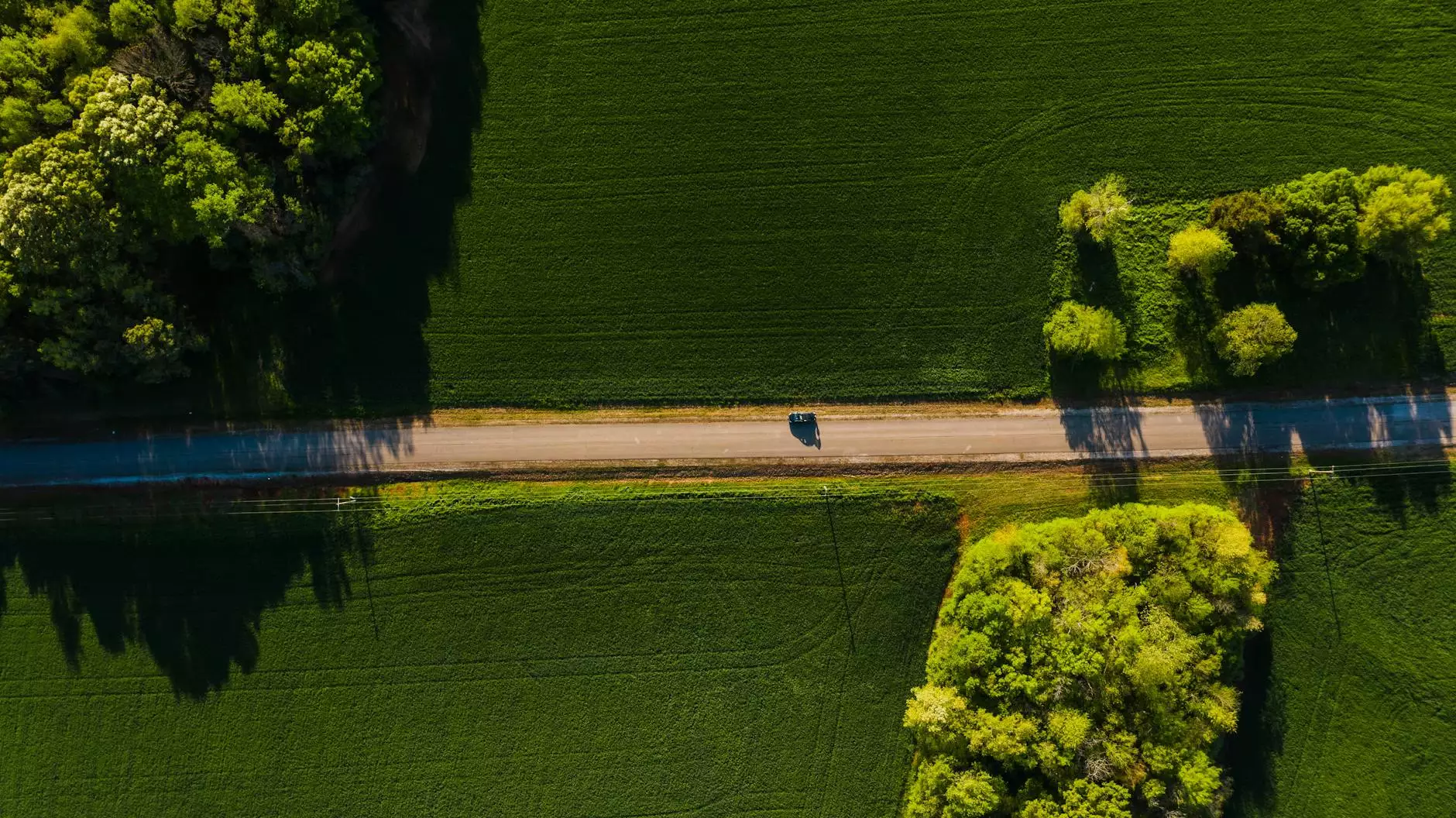
The automotive industry is undergoing a transformative shift, driven by advancements in technology, sustainability initiatives, and the increasing demand for efficiency. At the heart of this revolution are automotive plastic parts. These components not only play a critical role in the functionality of vehicles but also contribute significantly to their weight reduction, design flexibility, and overall performance. In this comprehensive article, we will explore everything you need to know about automotive plastic parts, their applications, benefits, and future trends.
What Are Automotive Plastic Parts?
Automotive plastic parts refer to components made from various plastic materials utilized in automobile manufacturing. These parts can vary widely in shape, size, and function, ranging from interior fittings to exterior panels. Common materials used for these parts include polypropylene (PP), polyethylene (PE), polyvinyl chloride (PVC), and acrylonitrile butadiene styrene (ABS), each selected for its specific properties and compatibility with different automotive applications.
Types of Automotive Plastic Parts
Automotive plastic parts are categorized based on their application. Here are some of the most prevalent types:
- Interior Components: Dashboard panels, center consoles, door trims, and seating components.
- Exterior Components: Bumpers, fenders, grilles, and wheel covers.
- Functional Parts: Housings for lights, mirror mounts, and components for air conditioning systems.
- Under-the-Hood Parts: Intake manifolds, fuel tanks, and other components that require heat resistance.
Benefits of Using Automotive Plastic Parts
The incorporation of automotive plastic parts in vehicle design offers numerous advantages:
- Weight Reduction: Plastics are lighter than metals, which contributes to overall vehicle weight reduction, enhancing fuel efficiency.
- Design Flexibility: Plastics can be molded into intricate shapes, allowing for innovative designs that may be difficult or impossible to achieve with metals.
- Corrosion Resistance: Plastics are inherently resistant to rust and corrosion, ensuring longevity and lower maintenance costs.
- Cost Efficiency: The manufacturing process for plastic parts often requires less energy and results in lower production costs.
- Noise and Vibration Damping: Plastics provide better sound insulation properties compared to metals, contributing to a quieter ride.
The Manufacturing Process of Automotive Plastic Parts
The production of automotive plastic parts involves several key processes:
Material Selection
The choice of material is pivotal to the performance and durability of the parts. Engineers evaluate the required mechanical properties, thermal stability, and aesthetic qualities to select the ideal plastic.
Molding Techniques
The most common manufacturing techniques include:
- Injection Molding: This process involves injecting molten plastic into a mold, allowing for high-precision and complex shapes.
- Blow Molding: Used for creating hollow plastic parts, this involves inflating a heated plastic tube until it conforms to a mold.
- Thermoforming: Sheets of plastic are heated until pliable and then formed over molds to create parts.
Finishing Techniques
After molding, parts may undergo various finishing processes, such as painting, coating, and plating, to enhance appearance and functionality.
Innovations in Automotive Plastic Parts
The automotive sector is in constant evolution, leading to innovative applications for automotive plastic parts. Here are some notable trends:
Biodegradable Plastics
With growing environmental concerns, the development of biodegradable plastics is on the rise. These materials can decompose under natural conditions, reducing the environmental impact at the end of life.
Lightweight Composites
Integrating plastics with other materials, such as carbon fibers, creates composites that provide superior strength-to-weight ratios. This trend is essential for meeting evolving fuel economy standards.
The Role of Deepmould.net in Automotive Plastic Parts Manufacturing
Deepmould.net stands at the forefront of the automotive plastic parts industry, combining innovative manufacturing techniques with a commitment to quality. As metal fabricators, their expertise in producing complex, high-precision plastic components positions them as a leader in automotive applications.
Quality Assurance and Testing
Quality assurance is crucial in the production of automotive components. Deepmould.net employs rigorous testing protocols to ensure that all plastic parts meet or exceed industry standards for safety and performance.
Custom Solutions
Understanding that each client has unique needs, Deepmould.net offers customized solutions tailored to specific automotive projects, ensuring that manufacturers receive the right components for their vehicles.
Challenges in the Automotive Plastic Parts Industry
Despite the advantages, there are challenges related to the use of automotive plastic parts. Some of these include:
- Recyclability: Although many plastics can be recycled, the process can be complex, and not all facilities accept them.
- Thermal Stability: Certain plastic components may not withstand extreme temperatures, necessitating careful selection based on the application.
- Market Fluctuations: The price of raw materials can vary significantly, impacting production costs and pricing strategies.
The Future of Automotive Plastic Parts
The outlook for automotive plastic parts appears robust as automakers increasingly seek sustainable and efficient solutions. The shift towards electrification in vehicles opens new avenues for innovation, with lightweight materials playing a critical role in enhancing battery efficiency and overall vehicle performance.
Integration with Smart Technology
As vehicles become smarter through the integration of technology, the demand for sophisticated plastic components is expected to grow. These parts will need to accommodate sensors, displays, and communication systems, requiring manufacturers to innovate continuously.
Conclusion
In conclusion, automotive plastic parts are indispensable in modern vehicle manufacturing, providing a blend of functionality, aesthetics, and performance. With ongoing advancements in technology and materials, such as those championed by Deepmould.net, the automotive industry is poised for a future where plastic components play an ever-increasing role in design, efficiency, and sustainability. Investors, manufacturers, and consumers alike should take note of these developments, as they represent the future trajectory of automotive engineering and innovation.